Accomplish Excellence: Advanced Techniques in Casting Aluminum
Accomplish Excellence: Advanced Techniques in Casting Aluminum
Blog Article
Opening the Potential of Light Weight Aluminum Spreading: A Comprehensive Overview
Light weight aluminum casting stands as a foundation in the realm of metalworking, using a wide range of advantages and applications throughout various sectors. From its historical value to the contemporary innovations in casting strategies, aluminum has actually constantly confirmed itself as a flexible and valuable material. As we browse with the landscape of light weight aluminum casting procedures and look into the intricacies of high quality control measures, a detailed review of unlocking real potential of this metal arises. The possibilities seem countless, promising understandings that can transform the means we make use of and view light weight aluminum in manufacturing (casting aluminum).
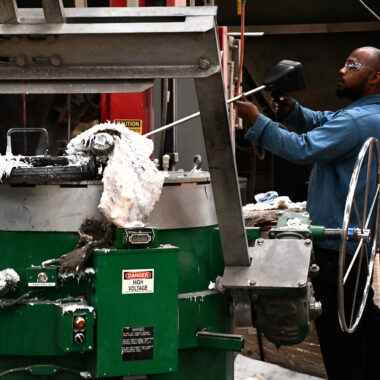
History of Light Weight Aluminum Spreading
Aluminum spreading has a rich historic background that dates back to ancient worlds, showcasing the withstanding significance of this metallurgical procedure in various markets. When ancient civilizations like the Egyptians and the Sumerians utilized fundamental methods to cast tiny objects, the origins of light weight aluminum spreading can be traced to around 5,000 B.C.. Nevertheless, it was not till the 19th century that aluminum casting saw considerable improvements with the discovery of the Hall-Héroult process for drawing out light weight aluminum from its ore, making it more available for casting functions.
During the Industrial Transformation, aluminum spreading obtained extensive appeal due to the metal's light-weight residential or commercial properties and rust resistance. This caused its extensive usage in making parts for numerous markets, consisting of automobile, aerospace, and building and construction. The versatility of aluminum casting permitted detailed designs and complex shapes to be generated with accuracy, further fueling its adoption across different industries. Today, aluminum casting continues to be a foundation in the production of a large variety of items, highlighting its enduring tradition and value in contemporary manufacturing processes.
Advantages and Applications
With its exceptional strength-to-weight proportion and outstanding thermal conductivity, aluminum spreading offers a myriad of benefits and diverse applications throughout various sectors. One of the key advantages of light weight aluminum casting is its light-weight nature, making it an optimal choice for markets where weight reduction is vital, such as automobile and aerospace. casting aluminum. In addition, aluminum spreading provides exceptional corrosion resistance, making certain sturdiness and long life in extreme atmospheres. Its high thermal conductivity also makes it a preferred choice for applications calling for warm dissipation, like in digital components and warm exchangers.
In terms of applications, aluminum casting is extensively made use of in the vehicle market for components like engine blocks, cyndrical tube heads, and wheels due to its toughness and light-weight homes. The flexibility of aluminum spreading prolongs to consumer electronic devices, where it is utilized in the production of coverings and warm sinks.
Types of Light Weight Aluminum Spreading Processes
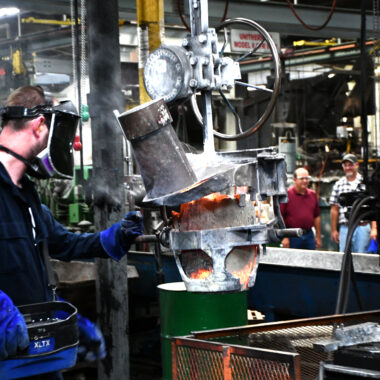
Amongst the different methods utilized in industrial settings, light weight aluminum casting procedures include an array of methods matched to different applications and needs. Investment spreading, also understood as lost-wax casting, is favored for its capacity to produce thorough and elaborate components with Continue a smooth surface area finish. Each of these light weight aluminum spreading processes uses unique advantages, providing to a wide variety of commercial needs.
Advancements in Light Weight Aluminum Casting Methods
Current advancements in aluminum spreading strategies have transformed the production sector, offering enhanced performance and accuracy in the production of complex elements. One remarkable innovation is the development of 3D sand printing innovation, which makes it possible for the production of intricate sand molds with minimal manual work. This method permits better design flexibility and faster production cycles, making it optimal for prototyping and little set manufacturing.
In addition, making use of innovative simulation software has click resources actually dramatically improved the casting process by allowing engineers to enhance mold designs and predict potential problems before production starts (casting aluminum). This causes boosted item high quality and minimized material waste
Furthermore, the adoption of vacuum-assisted aluminum spreading has actually enhanced the general quality of castings by minimizing porosity and making certain an extra consistent distribution of molten steel. This strategy is especially useful for components that require high architectural stability and exceptional surface coating.
High Quality Control in Aluminum Casting
The innovations in light weight aluminum casting strategies have not just improved performance and accuracy but have actually likewise underscored the critical relevance of high quality control in guaranteeing the integrity and efficiency of cast elements. Quality control in light weight aluminum casting entails a methodical approach to check and assess the manufacturing process, determining any variances from set criteria that could impact the end product.
One crucial element of quality assurance is making use of innovative innovations such as non-destructive screening methods like X-ray and ultrasound to find internal flaws without endangering the integrity of the cast components. Additionally, carrying out rigorous evaluation methods at various stages of manufacturing aids in identifying and remedying concerns quickly, making sure that just components satisfying the defined standards are released for use.
Moreover, quality assurance expands beyond the manufacturing process to include post-casting useful content treatments like warmth treatment and surface completing, ensuring that the end products fulfill the wanted specifications. By prioritizing quality assurance procedures, producers can improve product consistency, longevity, and overall client contentment in the world of light weight aluminum spreading.
Conclusion
To conclude, aluminum spreading has a rich history and uses many benefits and applications across different markets. Different kinds of casting processes and innovative techniques have been developed to enhance the efficiency and quality of light weight aluminum spreading. Quality assurance procedures play a vital duty in making sure the last products meet the called for criteria. On the whole, light weight aluminum casting continues to be a valuable production procedure with terrific potential for further innovations in the future.
As we navigate via the landscape of aluminum spreading procedures and delve right into the complexities of top quality control steps, a comprehensive review of unlocking the real potential of this steel emerges. It was not up until the 19th century that aluminum spreading saw significant improvements with the discovery of the Hall-Héroult procedure for extracting aluminum from its ore, making it extra easily accessible for casting purposes.
Among the numerous methods utilized in commercial settings, light weight aluminum spreading processes incorporate a range of methods matched to different applications and demands. Financial investment casting, likewise recognized as lost-wax casting, is favored for its capacity to produce elaborate and thorough components with a smooth surface finish. Different kinds of casting procedures and innovative methods have actually been created to enhance the efficiency and high quality of light weight aluminum spreading.
Report this page